Avoiding and rectifying common cutting problems.
There are several variables to consider when selecting a knife. Tooth pitch, tooth uniformity, quality of manufacture and material used are all important considerations.
Finish: The surface finish of the knife should be smooth, and the angles and pitch of the teeth should be uniform throughout. Material hardness is crucial and this can be retained by ensuring low-temperature grinding operation during the manufacturing process.
Tooth Pitch: Material build-up can often be caused by using the incorrect tooth pitch for the thickness of board being cut. Thicker board requires a greater tooth depth in order to avoid the knife penetrating through the board beyond the root of the tooth. This means a knife with fewer teeth per inch (TPI) should be considered when cutting thicker board (fig.6). A good knife supplier should be able to suggest the appropriate number of teeth per inch for your setup. While ideally an especially configured knife should be used for each thickness of board being processed, the reality for many plant managers is that frequently changing knives whenever the board thickness changes not possible. In this case, the most suitable number of teeth per inch to cover the range of boards produced on a particular line should be recommended.
Root gap: When setting up the knife unit, a ‘root gap’ of between 0.5mm and 1mm is recommended to prevent the knife penetrating the board beyond the root of the tooth. (see fig. 4) This reduces the likelihood of material build-up and metal-to-metal contact.
Material: High quality material is essential. The knives must be able to withstand rusting and corrosion due to the presence of salts and other additives in the gypsum mix – yet maintain a high level of hardness and toughness to avoid failure due to damage and excessive wear. The most suitable material for the manufacture of gypsum blades is therefore stainless steel.
Method of manufacture: The method of manufacture also affects the performance and longevity of the knife. For optimum performance, a precise and uniform tooth pitch must be achieved. Any two knives from the same manufacturer should be able to mesh perfectly together with no metal-to-metal contact.
Please contact Keith to discuss your requirements
Office: +44 (0) 114 244 0527 Ext: 152
email: keith.rowland@fernite.co.uk
Mobile: 07801 081952
WhatsApp: 07801 081952
Available
Mon – Thu: 8.30am – 5.00pm
Fri: 8.30am – 3.45pm
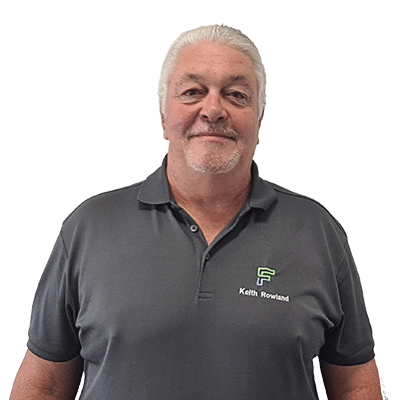
Fernite guidance for optimum blade performance
Tooth Pitch Range
Fernite gypsum blades are supplied in a range of tooth pitches, the industry standard tooth pitch options being 3tpi, 4tpi, 5tpi and 6tpi.
Choosing the correct tooth pitch for the thickness and type of board your plant produces can improve cutting performance.
Contact Keith on +44 (0) 114 244 0527 or email for a personalised recommendation for your plant.
A range of coatings available
Our long-life blades are available in a range of coatings, get in touch to see which one would suit you best.
+44 (0) 114 244 0527
We’re always here to help.
Our friendly, expert team are here to support your success.
If you have any questions about our gypsum blades, or would like a quote, please get in touch.
Call +44 (0)114 244 0527 or email
Alternatively, click below to complete our online enquiry form.
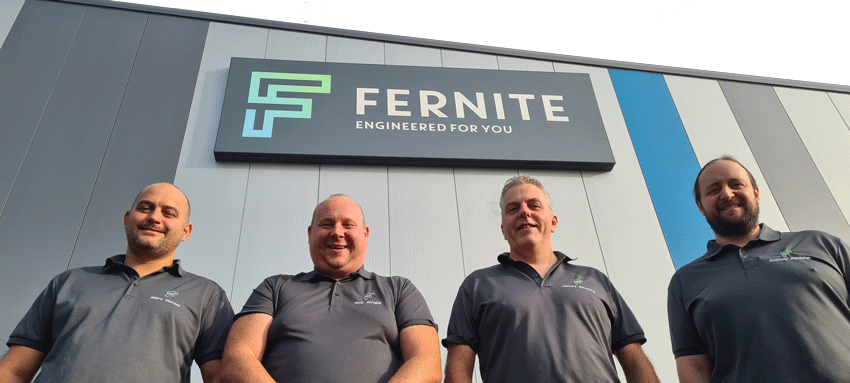